Scott Martin's Digital Imaging Newsletter
Thoughts, news and techniques for digital imaging professionals
|
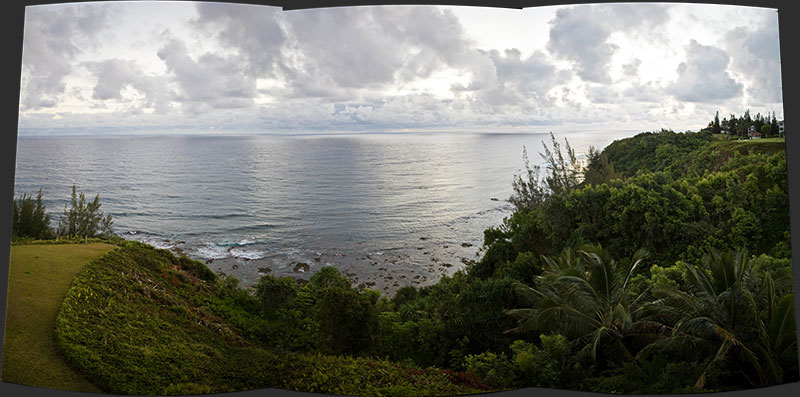
Kauaian Landscape, June 2007
|
|
July Printmaking Workshop in Santa Fe
I will be teaching a "Color Management and Digital Printing" workshop at the New Mexico Photography Field School in Santa Fe July 21st and 22nd. This two day lecture/demonstration will take an advanced look at the skills necessary for high quality digital fine art printing. We will examine the history of digital fine art printing processes, and look at all the processes available today including those often overlooked. Special attention will be paid to black-and-white printing alternatives. Participants will learn about RIPs, ink technology, terms like metamerism and bronzing, and media recommendations. We will have example prints on all the latest fiber base inkjet papers (Innova F-Type, Crane Silver Rag, Hahnemuhle Pearl, Moab Colorado, etc.).
Color management at every stage of the digital imaging workflow will be covered. We will look at the calibration packages currently available, and learn some unconventional ways for calibrating monitors and profiling digital printers to obtain exceptional printing. We will take an in-depth look at sRGB, AdobeRGB, ProPhotoRGB: what they are, why bigger is not always better, and how you should choose your own working space. This will be a lecture and demonstration workshop, no computer is required.
|
|
G7 method Press Calibration
G7 is a proof-to-print process developed by the IDEAlliance that uses spectrophotometry to calibrate presses by the numbers to specifications like SWOP, GRACoL or FOGRA. Previous press calibration methods relied upon basic densitometry, dot gain and visual analysis and could take days of press runs and tweaking to get done fairly well. Because of the ambiguity and expense of these older methods most print shops don't even bother. It is extremely common in this day and age for print shops to claim they "print to SWOP" when they haven't taken any steps to calibrate to SWOP. Platesetter calibration is often confused with SWOP calibration. Ask a print shop to show your their SWOP (or GRACoL or FOGRA) calibration test results and most of them won't know what you are talking about. Print shops have had to put up with a variety of customer complaints and salesmen constantly showing up with all kinds of solutions to their problems. While I can't blame them for their thick skin, I believe G7 is their real solution. Without calibration every press prints differently which leads to poor proofing, long press checks and less than optimal final results.
IDEALinkCurve is new a software application that simplifies G7 press calibration without the tedium and uncertainty of manual curve editing. Not only does it provide the RIP curves necessary for accurate printing but it provides a wealth of new ways to analyze color, hue, TVI and gray balance. The G7 method combined with IDEALinkCurve allows someone like myself to calibrate a press extremely accurately in hours instead of days.
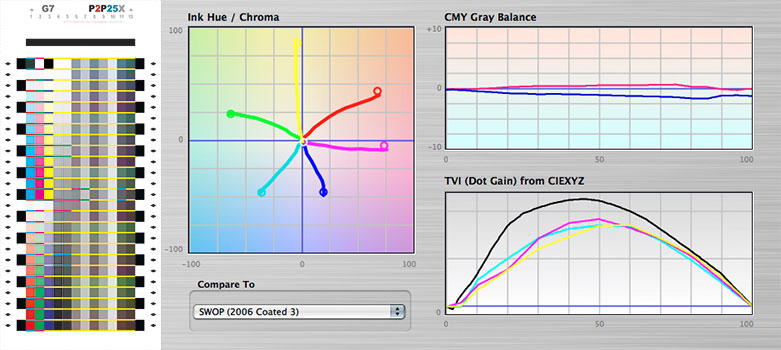
I have started calibrating presses this way and am really excited about it. We have had spectrophotometry-based methods of calibrating inkjet and photo paper printers for years so it's great to finally see the offset industry get up to speed with well adapted techniques for calibrating "the devil's color mode" (CMYK).
I think it is time for a big call to arms for everyone in the printing industry (art directors, designers, print brokers, prepress professionals and print shop owners) to educate themselves about G7 method press calibration. Art directors, designers, and print brokers should start asking their print vendors if their presses are calibrated, and if so, with what method. Print shop owners and prepress professionals that embrace G7 calibration with an open mind might find that it's what they've been looking for throughout their career. Print shops can empower their sales staff with their own SWOP calibration results and samples to show to existing and prospective customers.
Well calibrated presses translate into lower operating costs, faster press ready times, reduced or eliminated press checking, better press to press matching, better proof to print matching, reduced makeovers and most importantly, optimal quality. It is in all of our best interests to calibrate our presses, work with those who do and encourage those who are not yet doing so.
Download the Calibrating, Printing and Proofing by the G7 Method PDF for some excellent reading on this process. I also have a collection of related offset printing links on my Links page.
|
|
ProofLine Press White Proofing paper now available
I have searched high and low for an excellent inkjet paper for offset press proofing. Most inkjet papers are designed for maximum gamut and black Dmax rendering. In comparison to what we typically see on press these papers have a much brighter white, a much larger color gamut and a higher, richer DMax. What’s worse is that these papers don't feel like offset stock and are typically too glossy or too matte.
Making inkjet paper specifically for offset proofing is a speciality process. Epson’s Semimatte Commercial Proofing paper is disappointingly yellow in comparison to most offset paper stocks used today that contain a modest amount of optical brighteners. There is a whole new generation of very similar proofing papers from EFI, GMG, MidStates Graphics and a few others that look nearly identical to common coated offset stocks. I’ve tested and compared these papers side by side on a variety of printers and have decided that ProofLine Press White is the paper best suited for my clients. It is available in all common sizes and appropriate for photographers, designers, ad agencies and print shops.
I am shocked at the generally poor quality of proofs made today and am encouraging all of my clients to invest in this paper for their proofing needs. This paper isn’t yet available through any online resellers or any retail outlets. ProofLine papers are traditionally only sold through the distribution channels that print shops get their supplies from. So that all of my clients can easily get their hands on this paper, I’ve arranged for a distributor to sell this paper direct to Onsight clients at a 10%-20% discount. I have created custom pricing and order form PDFs that my clients should use when placing these orders. They are great to deal with and very prompt.
Download the ProoLine Pricing PDF
Download the ProoLine Order Form PDF
I think you'll find this paper can significantly enhance the quality of your proofs. As always I am available to show you print samples or to calibrate this paper on your own printer. Let me know if I can help.
|
|
Feedback
As always, I love to hear from you. Please drop me a line and let me know how everything is going for you. Comments and suggestions for this newsletter are appreciated too.
Scott Martin
scott@on-sight.com
www.on-sight.com
|
© Scott Martin - Digital Imaging Training and Consulting - 210.224.1113 - www.on-sight.com
The contents of this page may not be reproduced in any form without written permission.
|